HM Quickshifter GP
A basic
quickshifter works by killing of the ignition for a certain period of time in
order to relieve stress on the gear box, thus allowing the pressure on the gear
lever / selector drum to slip the transmission into the next gear without
grinding or chipping gear teeth / dogs.
The ignition kill time is a
somewhat crude parameter as one kill time for each gear must cover all gear
changing eventualities / loads / rpm / rider actions – to this end we have
developed the HM Seamless Shift algorithm.
The new HM Quickshifter GP
has rewritten the rules when it comes to gear changing, the result being the
most accurate, fastest, smoothest safest quickshifter by far.
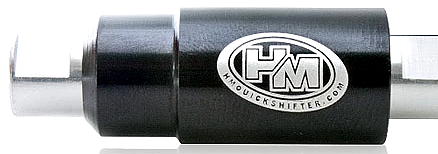
HM
SEAMLESS SHIFT
-
USING GEAR DOG ENGAGEMENT DETECTION (HMSS)
The HM GP
Shifter has programmable kill times for each gear going up and separately going
down the gearbox. However on top of this we have the new revolutionary HMSS
system. This system uses intensive and very advanced mathematics and digital
signal processing (DSP) to identify when the actual dogs / gears have fully
engaged. This nullifies the requirement for kill times and not only ensures the
shorted possible kill times it also ensures the smoothest and safest gear
change.
This is because regardless of
the conditions / load / RPM / gearbox characteristics, it detects when the next
gear is actually engaged and then reapplies power. This is a massive step
forwards in shifting technology and has made all other shifting products
obsolete.
There are also safety programmable
minimum and maximum kill times which over ride this algorithm in the rare case
that the rider/bike is doing something very unusual and for some reason the
shifter does not correctly detect this gear engagement in a timely fashion.
Typically a kill time is a crude parameter that must be significantly longer
than the actual gear change time due to the vast range of different gear
changing conditions, this directly translates to slower lap times, less smooth
gear changes, more wear on the gearbox and the potential for a missed gear if
the rider / bike do something unusual and end up taking longer to mechanically
shift than the allowed kill time.
In short – a revolution in changing gears! Not just a
gimmick – this is the culmination of thousands of hours of work by contracted in
specialists in their field.
FEATURES
AT A GLANCE
-
Fully and continuously dynamic
self learning, very fast and incredibly accurate gear determination
-
HMSS System beats chosen shift times to save
significant accumulated time over a lap and provide seemingly seamless
shifts
-
Multiple types of outputs, all easily programmable
-
Built in full feature Blipper controller for
down-shifting in conjunction with any external blipper module (not available
from HM)
-
Each gear has its own kill time and its own
sensitivity
-
Microsecond accuracy on kill times
-
Highly intelligent real time fault analysis and
configurable error strategy. Policy: never allow even a smashed shifter to
cause total motorcycle failure
-
Easily readable, detailed and cyclic event log
-
Data logging
-
Firmware updateable via USB
-
Highly sophisticated feedback derived kill time
augmentation – unbeatable for laptime saved
-
Advanced feedback derived power cutting / introduction
strategies (under development)
-
RPM kill time bias (under development)
-
LIN Interface to allow connection to ECU’s / Dashes
for delivering data, recording data, and in-the-field configuration
adjustments without a computer
-
CAN / ECAN Interface via optional CAN transceiver
(under development)
-
Simple USB interface (No Drivers! Just plug into any
Windows Operating System and play!)
-
Very Low power for a heavy weight 32bit RISC processor
(30mA)
-
Highly resilient power supply, able to operate up to
80v and can withstand transients far in excess of automotive standards
-
Very small size
-
Low Cost
-
HM’s 24/7 professional support
-
Ultra light weight
DERIVING
GEAR POSITION
This brought on its own challenges, in particular correctly detecting the gear
position. If the shifter is going to be our flagship product, then it must
operate with the same unbreakable robustness and absolute consistency that our
current shifters are renowned for. The trouble is that something seemingly as
simple as calculating gear position is, in fact, a very difficult challenge. The
way most existing such devices work (including our HM Dash) is by comparing the
ratio between speed and RPM to derive gear. This is fine for a dash display but
not, in our view, good enough for a high precision device that relies on
perfectly correct information. Chain chatter, firing order, rev limiters, clutch
clip and traction control can all fool this type of calculation.
The problem is actually worse
than it initially seems. Take for example 6th gear. If the bike is in 6th gear
then it would be desirable to prevent a shift from happening if the rider
inadvertently tries to select a non-existent 7th gear. This is something we know
many riders do – something that we have seen in data logging time and time
again. The purpose, of course, is to prevent a time- and power-killing “false”
shift if the rider does this. But what happens if the bike is actually in 5th
and the shifter is “one off” and thinks it is in 6th? The rider will be
prevented from shifting to 6th – not acceptable by any measure, and by using
current techniques this is a very real danger.
Another example is the shift
from 1st to 2nd. On most gear boxes the kill time required for 1st to 2nd gear
changes is significantly longer than from 2nd to 3rd for example. So again, if
the bike is in 1st gear but the shifter thinks it is in second gear, then a very
rough or missed shift may take place, likely causing gearbox damage!
Also consider the case of
short shifting or multiple fast gear changes (with or without clutch): again
current calculation techniques are relatively slow, so this is yet another area
that the shifter could be fooled. As the astute reader may have surmised, this
is NOT just a matter of adding 1 for each up-shift, and subtracting 1 for each
down-shift! The gear actually must be verified with no assumptions made.
Add all of this together and it is easy to see our
hesitation in including this in a product where absolute consistency for
professional use is paramount.
While is it true that there are ways of
“smoothing over” or masking current techniques so that the effect is, on the
whole, acceptable – these do not give the kind of confidence in a product that
we have become used to, or as demanded (and expected) at the highest levels of
racing.
After a lot of research by some very highly
qualified people we put together a technical specification that demanded 100%
accuracy with respect to gear position. Part of this specification was that even
99.99% was not good enough. Another requirement for gear position was that the
shifter needed near instant results in real time – a big requirement! A team of
mathematical engineering specialists worked on this problem for nearly two
years.
The answer lay in use of predictive mathematics, namely in the form of a
specially-adapted non-linear time domain version of a Kalman Algorithm – the
same type of math that predicts financial markets, tracks fast-moving military
targets, and steers missiles. A sledge hammer to crack a nut? Perhaps, but it
works, and it works wonderfully.
When a gear change is made, the result – measured and verified without any
assumptions – is accurately computed within 2-3 meters of completion of the
shift. At 250 KMH, the typical delay between the completed shift and the gear
being known with certainty is measurable in milliseconds! THAT is world class,
and as far as we know, hasn’t been achieved anywhere else in the world. That
compares to bikes with built in analog-type rotary gear position sensors!
We have pumped hundreds of thousands of
logged simulation, road, and race miles through the GP shifter and have had a 0%
failure rate.